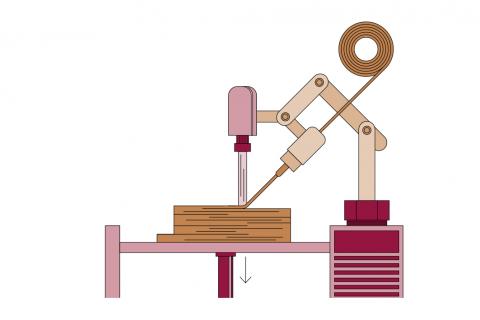
Vers un nouvel essor de la fabrication additive
(Cet article est tiré de L'Édition n°19)
Plusieurs laboratoires de l’Université Paris-Saclay articulent leurs recherches autour de la fabrication additive et de l’usine du futur. Cela comprend l’optimisation des procédés, le contrôle des pièces et le développement de nouveaux processus de fabrication.
Prothèses médicales, voitures, maisons, satellites… La liste des objets dont la fabrication est aujourd’hui envisageable par impression 3D, ou fabrication additive (FA), ne cesse de s’allonger. Si le premier dépôt de brevet date de 1984, l’essor de la technologie n’intervient réellement qu’au mitan des années 2000, avec la levée progressive des brevets entourant ses procédés et la commercialisation des premières imprimantes 3D. Au début, celles-ci ne sont utilisées qu’à des fins ludiques avant de servir à du prototypage rapide.
Mais que ce soit dans le domaine de la bioimpression, des transports, de l’architecture, du design et bien d’autres, les industriels se rendent vite compte des nombreux avantages de cette technologie. La FA libère la créativité des concepteurs (en optimisant les formes et les propriétés des pièces fabriquées) autant qu’elle fait baisser les coûts de production (en réduisant les pertes de matière ou le nombre de pièces à fabriquer). Depuis 2015, son marché mondial connaît un essor exponentiel et la production industrielle compte aujourd’hui sur elle pour développer l’industrie du futur. En lien avec cette thématique, plusieurs laboratoires de l’Université Paris-Saclay travaillent sur l’optimisation de ses procédés et la qualité des pièces fabriquées.
De multiples procédés de fabrication
La FA est une fabrication de pièces en volume qui repose sur l’ajout de matière, couche par couche, à partir d’une modélisation numérique 3D réalisée par un logiciel de conception assistée par ordinateur (CAO). Elle comprend sept classes de procédés : photo-polymérisation en cuve, projection de matière, projection de liant, fusion sur lit de poudre, extrusion de matière, dépôt de matière sous flux d’énergie dirigé, et stratification de couches. Le choix du procédé utilisé se fait en fonction du type de matériau (polymères thermodurcissables ou thermoplastiques, bois, métaux, céramiques), de la taille finale de la pièce, de la finesse de réalisation ou du rendement souhaités. Pour la réalisation de pièces métalliques, particulièrement à l’étude au sein des laboratoires de l’Université, les procédés par fusion de matière sont souvent privilégiés car ils affichent une meilleure productivité. La fabrication se fait alors par dépôt de fil fondu, par dépôt de poudre ou par fusion sur lit de poudre.
Des nouveaux matériaux…
Au sein de la plateforme Saclay’s Advanced Manufacturing and Technological Applications (SAMANTA) du CEA Paris-Saclay, les scientifiques s’intéressent plus spécifiquement aux procédés dits de dépôt d’énergie concentrée (Direct Energy Deposit ou DED) par laser ou faisceau d’électrons sur poudre ou sur fil, et de fusion laser sur lit de poudre (Laser Powder Bed Fusion ou LPBF). Ils s’attachent à mettre au point de nouveaux alliages ou à contrôler les propriétés physico-chimiques d’un matériau au regard de son application finale.
Aujourd’hui, la FA devient aussi et de plus en plus une brique technologique pour découvrir de nouveaux matériaux et l’équipe de SAMANTA tourne son regard vers les poudres métalliques. Elle cherche à mettre au point des matériaux à haute entropie, également appelés alliages à cinq éléments (au choix parmi le fer, le cobalt, l’aluminium, le chrome, le tungstène, le titane, le molybdène…). Dans le cadre du Programme et équipements prioritaires de recherche (PEPR) DIADEME, elle compte sur l’intelligence artificielle (IA) pour l’aider. « Il s’agit d’abord de synthétiser un grand nombre d’échantillons grâce au procédé DED pour ensuite réaliser un screening rapide de leurs propriétés. Le grand volume de données généré sera alors traité par IA », développe Hicham Maskrot, responsable du Laboratoire d’ingénierie des surfaces et laser au sein du Département de physico-chimie (Univ. Paris-Saclay, CEA).
… aux comportements originaux
Car la FA induit des phénomènes qui n’existaient pas auparavant. Elle crée dans les matériaux des microstructures inédites. La FA permet par exemple de créer des métamatériaux (des matériaux artificiels à structure périodique). Les recherches réalisées au sein de SAMANTA ont ainsi débouché sur la mise au point de filtres métalliques dont les procédures de fabrication étaient auparavant assez lourdes. Dans la continuité de ces travaux, la start-up AME2L, en cours de création, mettra au point des métamatériaux à destination d’industries du domaine de la filtration, des amortisseurs de chocs et de l’énergie.
« Du fait de processus de solidification très rapides, les atomes constitutifs de la matière s’arrangent de façon très spécifique, explique Hicham Maskrot. Il s’agit maintenant de déterminer si ces phénomènes confèrent au matériau un comportement particulier et de voir comment jouer sur sa composition. Le matériau fabriqué est-il par exemple plus résistant à la corrosion ou à l’irradiation qu’un matériau classique ? » En lien avec ces questions, SAMANTA répond aux besoins d’équipes de recherche et d’industriels travaillant sur le mix énergétique.
Obsolescence, réparation et suivi d’usure
Dans ce domaine, la FA se montre particulièrement utile pour répondre à la problématique de l’obsolescence des pièces par rétro-conception. En partant d’une ancienne pièce, dont le plan original est manquant, et en la scannant, il est possible de la refabriquer par FA. « La technique de LPBF permet de réparer sur site, localement, la pièce endommagée », souligne Hicham Maskrot.
Il est également possible d’insérer des traceurs (fibres optiques, capteurs chimiques ou de déformation) dans les objets : ils fournissent des informations sur l’état et le comportement du matériau et des contraintes subies (température, irradiation, fissure…) tout au long de la vie des objets. « La FA favorise le développement d’objets intelligents. En mettant par exemple des luminophores ou des fibres optiques dans un acier 316L, le matériau le plus utilisé dans l’industrie nucléaire, on vérifie en temps réel dans quel état il se situe. On sait quand il faut changer la pièce et la remplacer uniquement lorsqu’elle est usée », commente Hicham Maskrot.
La nécessaire qualification des pièces
Mais comme toute technologie récente, la FA n’est pas exempte de quelques verrous. Ils concernent la productivité des machines, la taille des pièces et surtout, leur qualification. Au Laboratoire de méthodes de contrôle du CEA-List, l’équipe de Steve Mahaut travaille à mieux maîtriser le contrôle des pièces fabriquées, afin de mieux qualifier les pièces finies. « Aujourd’hui, les constructeurs disposent de données de monitoring : il s’agit d’un rapport de fabrication attestant que celle-ci s’est bien déroulée et que les consignes d’utilisateur ont été respectées. Il reste à vérifier que la pièce fabriquée est conforme, exempte de défauts tels que porosité, manque de matière, fusion inadaptée, » relate Steve Mahaut.
Pour autant, ces données suffisent-elles à garantir la bonne conformité de la pièce ? Car même en maîtrisant tous les paramètres de la machine (température, vitesse, puissance du laser, etc.), des phénomènes liés aux procédés eux-mêmes perturbent la fabrication. Par exemple, dans le cas du procédé arc-fil (Wire Arc Additive Manufacturing ou WAAM), la distance entre la pièce et la torche (l’arc-fil) change en cours de fabrication, car la pièce se déforme avec la chaleur et le temps. Si la distance s’allonge, cela entraîne une moins bonne fusion de deux plaques de soudage. Dans le cas des procédés en fusion laser, des grains de poudre éjectés peuvent faire écran et conduire à une mauvaise fusion.
C’est pour cela que l’équipe du CEA-List développe des capteurs qui suivent la pièce au cours de sa fabrication, complémentaires aux outils existants et basés sur des méthodes électromagnétiques, ultrasons sans contact ou radiographiques. Tout l’enjeu est là : développer des capteurs les plus sensibles possibles aux informations les plus pertinentes, et établir une corrélation intelligente entre l’ensemble des données physiques recueillies et la réalité des pièces fabriquées. « De cette façon, si on voit en temps réel que, pour une pièce, un matériau et une machine donnés, les paramètres garantissant la bonne conformité de la pièce ne sont pas respectés, on peut soit décider d’arrêter la fabrication, soit – et c’est l’objectif ultime de la FA – corriger la pièce en cours de fabrication », signale Steve Mahaut.
La qualification au cœur de projets
C’est à ces fins que son équipe participe à plusieurs projets de recherche collaboratifs français (au sein de l’Additive Factory Hub sur le plateau de Saclay) et européens comprenant chacun un large consortium d’acteurs académiques et industriels. Le projet INTEGRADDE, qui tourne autour de la fabrication, par procédé DED, de pièces métalliques certifiées, vise à mettre au point un pipeline intelligent piloté par les données. Cette solution numérique intégrera les données de conception de la pièce (CAO), celles de fabrication (trajectoire du laser et stratégie appliquées), celles enregistrées lors de la fabrication et celles de contrôle, la pièce finie.
Centré sur le procédé WAAM, le projet GRADE2XL a pour objectif d’obtenir de grandes pièces bi-matériaux. « L’idée est de maîtriser localement, dans les zones exposées ou chargées mécaniquement, des propriétés matériaux (dureté, résistance à la corrosion) spécifiques », commente Steve Mahaut. Enfin, avec le projet NUCOBAM, ce sont le contrôle des pièces en post-fabrication et leur qualification en vue d’une utilisation dans le domaine du nucléaire qui sont à l’étude.
Un robot qui en dit long
Au Laboratoire universitaire de recherche en production automatisée (LURPA – Univ. Paris- Saclay, ENS Paris-Saclay), des chercheurs et chercheuses s’intéressent également à la qualité des pièces issues de la FA. Leur qualification passe par la mesure, en une, deux ou trois dimensions et au moyen d’instruments de métrologie, de l’écart de forme et de dimensions des pièces fabriquées, afin de planifier les éventuelles opérations de post-traitement à réaliser. En accord avec une industrie 4.0, leurs travaux visent à intégrer cette étape de mesures directement dans la ligne de fabrication des pièces. Ils développent pour cela une solution basée sur un robot anthropomorphe – reproduisant les mouvements d’un bras humain – combiné à un capteur laser.
« En mettant des capteurs laser sur une chaîne de montage ou sur un robot, et en faisant bouger soit le laser soit le bras du robot qui maintient la pièce, on obtiendrait des informations afin de qualifier la pièce en vol. Cela éviterait d’avoir à stopper la chaîne pour opérer ces mesures de contrôle. Et si une dérive se faisait sentir, on saurait qu’il faut modifier le procédé de fabrication », explique Olivier Bruneau, directeur du LURPA.
Caractériser les défauts pour parfaire la fabrication
Un robot présente toutefois une grande flexibilité articulaire et (dans une moindre mesure) segmentaire, des jeux, des frottements, des problèmes de parallaxes, de vibration, de petites erreurs de dimensions géométriques… Ce qui engendre au final des problèmes d’exactitude et de répétabilité de la trajectoire. Au LURPA, les scientifiques tentent de caractériser l’ensemble de ces défauts. Leur but est de proposer de nouvelles méthodes de modélisation intégrant numériquement ces défauts afin d’obtenir la meilleure trajectoire initiale possible.
Depuis peu, le laboratoire dispose d’une cellule robotisée hybride de fabrication additive/ soustractive. Un premier robot anthropomorphe y assure la fabrication d’une pièce grâce au procédé WAAM, tandis qu’un second bras robotique usine la pièce. « Celle-ci ne bouge pas de son support entre les étapes, ce qui diminue les erreurs et fait gagner du temps », signale Olivier Bruneau. Des caméras, disposées dans l’espace, assurent le suivi et contrôlent la bonne exécution des procédés. Les premières expériences ont démarré.
Mais fabriquer une pièce en FA à l’aide d’un robot est un vrai challenge. « Trois grands paramètres régissent cette fabrication : la vitesse à laquelle le fil métallique descend et sort de l’embout alimentateur, la puissance laser utilisée par la torche pour faire fondre le fil, et la vitesse d’avancée du robot. La corrélation des trois modifie la qualité de la pièce fabriquée, détaille Olivier Bruneau. Il nous faut donc déterminer l’influence de chacun des paramètres du procédé, puis faire de même avec les défauts du robot pour enfin estimer l’influence du couplage de l’un avec l’autre. Cela engendre une explosion combinatoire pour laquelle l’intelligence artificielle nous aidera à identifier les bonnes zones de fabrication de la pièce. »
La fabrication additive n’a décidemment pas fini de se réinventer.
Publications
- M. Nussbaum, et al. Mechanical properties and high temperature oxidation resistance of (AlCrTiV) N coatings synthesized by cathodic arc deposition. Surface and Coatings Technology, Vol. 434, 2022.
- Matthias Bordron et al. Inline measurement strategy for additive manufacturing. Proceedings of the Institution of Mechanical Engineers, Part B: Journal of Engineering Manufacture, Vol. 233 (5), 1402-1411, 2019.